Operations Analyst Job Duties: 50 Essential Responsibilities in 2023
Operations analysts are vital members of any organization, playing a crucial role in improving efficiency, productivity, and profitability. Their responsibilities encompass a wide range of tasks, from analyzing data to developing recommendations for process improvements.
In this comprehensive guide, we will explore the top 50 operations analyst job duties in 2023, providing a detailed overview of the essential skills and responsibilities required for this in-demand role.
Key Responsibilities of an Operations Analyst
-
Analyze Key Performance Indicators (KPIs): Monitor and track key metrics such as sales, revenue, and production levels to identify trends and areas for improvement.
-
Develop and Implement Process Improvements: Analyze existing processes to identify inefficiencies and bottlenecks, and develop and implement solutions to streamline operations.
-
Conduct Root Cause Analysis: Investigate problems and identify the root causes to prevent future occurrences.
-
Model and Simulate Processes: Use mathematical models and simulations to analyze and predict how operational changes will impact the organization.
-
Forecast Demand and Supply: Utilize historical data and predictive analytics to estimate future demand and supply levels to ensure efficient resource allocation.
-
Manage Inventory and Supply Chain: Optimize inventory levels and manage the supply chain to minimize costs and maximize efficiency.
-
Ensure Compliance with Regulations: Monitor and ensure compliance with industry regulations and standards related to operations.
-
Develop and implement quality control measures: Establish and implement quality control measures to ensure that products and services meet customer expectations.
-
Train and Develop Operations Staff: Provide training and development opportunities to operations staff to improve their skills and knowledge.
-
Manage Operations Budgets: Develop and manage operations budgets to ensure financial efficiency and cost control.
-
Conduct Performance Reviews: Conduct performance reviews for operations staff to identify areas for improvement and provide feedback.
-
Manage Vendor Relationships: Build and manage relationships with vendors to ensure timely delivery of goods and services.
-
Identify and Implement Technology Solutions: Identify and implement technology solutions to improve operations efficiency and reduce costs.
-
Collaborate with other Departments: Collaborate with other departments such as sales, finance, and marketing to align operations with organizational goals.
-
Stay Updated on Industry Best Practices: Continuously research and stay updated on industry best practices to implement the latest trends and technologies.
-
Develop and maintain standard operating procedures (SOPs): Define and document SOPs to ensure consistency and efficiency in operations.
-
Analyze and troubleshoot operational issues: Identify and resolve operational issues promptly to minimize disruptions and maintain optimal performance.
-
Manage project scope and timelines: Manage the scope and timelines of operational projects to ensure timely completion and successful implementation.
-
Prepare and present operational reports: Prepare and present operational reports to management and stakeholders to provide insights and inform decision-making.
-
Conduct variance analysis: Perform variance analysis to identify deviations from planned targets and take corrective actions.
-
Implement lean manufacturing principles: Implement lean manufacturing principles to reduce waste and improve efficiency.
-
Design and implement continuous improvement programs: Design and implement continuous improvement programs to drive performance excellence.
-
Conduct time and motion studies: Conduct time and motion studies to improve process efficiency and productivity.
-
Develop and maintain operational dashboards: Develop and maintain operational dashboards to provide real-time visibility into key performance indicators.
-
Conduct risk assessments: Identify and assess operational risks to develop mitigation strategies.
-
Develop and implement disaster recovery plans: Develop and implement disaster recovery plans to ensure business continuity in the event of disruptions.
-
Manage emergency response: Coordinate emergency response efforts to minimize disruptions and ensure the safety of employees and assets.
-
Conduct audits and inspections: Conduct audits and inspections to assess compliance, identify areas for improvement, and ensure operational effectiveness.
-
Participate in cross-functional teams: Participate in cross-functional teams to facilitate collaboration and drive organizational initiatives.
-
Stay informed about industry trends and best practices: Stay informed about industry trends and best practices to continuously improve operational performance.
-
Use data analytics tools and techniques: Use data analytics tools and techniques to analyze operational data and identify insights.
-
Communicate effectively with stakeholders: Communicate effectively with stakeholders at all levels to provide updates, share insights, and manage expectations.
-
Develop and implement training programs: Develop and implement training programs for operations staff to enhance skills and knowledge.
-
Monitor and maintain operational systems: Monitor and maintain operational systems to ensure smooth functioning and minimize downtime.
-
Identify and implement safety measures: Identify and implement safety measures to prevent accidents and injuries in the workplace.
-
Investigate and resolve customer complaints: Investigate and resolve customer complaints to maintain customer satisfaction.
-
Manage and maintain inventory: Manage and maintain inventory levels to ensure optimal stock levels and minimize waste.
-
Plan and coordinate logistics: Plan and coordinate logistics to ensure efficient and timely delivery of goods and services.
-
Conduct capacity planning and analysis: Conduct capacity planning and analysis to ensure that operations can meet demand.
-
Manage and monitor production schedules: Manage and monitor production schedules to ensure timely completion of orders and minimize disruptions.
-
Implement quality control measures: Implement quality control measures to ensure that products and services meet specifications and customer requirements.
-
Conduct performance evaluations: Conduct performance evaluations for operations staff to assess their progress and provide feedback.
-
Develop and implement incentive programs: Develop and implement incentive programs to motivate and reward operations staff for outstanding performance.
-
Participate in continuous improvement initiatives: Participate in continuous improvement initiatives to identify and implement ways to enhance operational efficiency.
-
Use technology to improve operations: Use technology to improve operational efficiency, such as automation, data analytics, and predictive maintenance.
-
Collaborate with other departments: Collaborate with other departments, such as sales, marketing, and finance, to ensure that operations are aligned with the organization's goals.
-
Stay up-to-date on industry best practices: Stay up-to-date on industry best practices by attending conferences and reading industry publications.
-
Maintain a safe and efficient work environment: Maintain a safe and efficient work environment by adhering to safety regulations and implementing best practices.
-
Develop and implement training programs: Develop and implement training programs to ensure that operations staff are equipped with the necessary skills and knowledge.
-
Provide feedback and support to operations staff: Provide feedback and support to operations staff to help them develop and improve their performance.
Additional Tips for Success
1. Develop Strong Analytical Skills: The ability to analyze data and identify trends is essential for operations analysts.

2. Stay Informed about Industry Trends: Keep up with the latest trends and best practices in operations management to stay ahead of the curve.
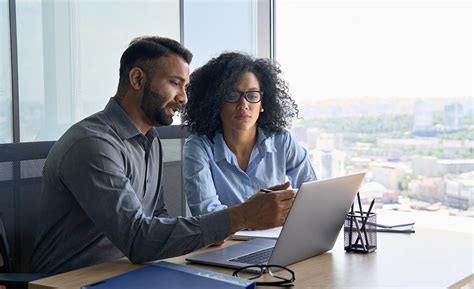
3. Embrace Technology: Leverage technology to improve operational efficiency and enhance your decision-making process.
4. Build Strong Communication Skills: Communicate effectively with stakeholders at all levels to share insights and influence decision-making.
FAQs
1. What is the average salary for an operations analyst?
According to the U.S. Bureau of Labor Statistics, the median annual salary for operations research analysts was $83,230 in May 2021.

2. What are the job growth prospects for operations analysts?
The U.S. Bureau of Labor Statistics projects that the job market for operations research analysts will grow 25% from 2021 to 2031, much faster than the average for all occupations.
3. What are the educational requirements for becoming an operations analyst?
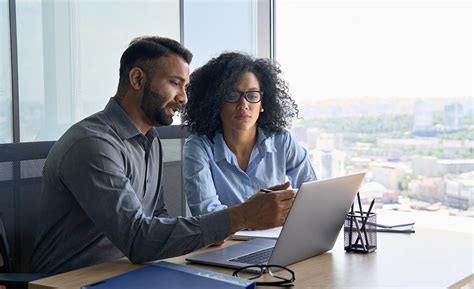
Most operations analysts have a bachelor's degree in a field such as operations research, industrial engineering, or business administration.
4. What certifications are available for operations analysts?
The Institute for Operations Research and the Management Sciences (INFORMS) offers the Certified Analytics Professional (CAP) certification for operations analysts.
5. What is the future of operations analysis?
The future of operations analysis is bright, as the demand for data-driven decision-making continues to grow. Operations analysts will play a critical role in helping organizations improve their efficiency, productivity, and profitability.
6. What are the top challenges facing operations analysts?
Some of the top challenges facing operations analysts include:
- Dealing with large and complex data sets
- Keeping up with the latest trends and technologies
- Communicating effectively with stakeholders at all levels
- Managing multiple projects simultaneously
7. What are the top trends in operations analysis?
Some of the top trends in operations analysis include:
- The use of artificial intelligence (AI) and machine learning to improve decision-making
- The adoption of lean manufacturing principles to improve efficiency
- The increasing use of data analytics to identify trends and patterns
8. What are the top skills for operations analysts?
Some of the top skills for operations analysts include:
- Analytical skills
- Data analysis skills
- Problem-solving skills
- Communication skills