101 Guide to Fertilizer Disc Granulation Machine: Unlocking a World of Granular Goodness
Fertilizer Disc Granulation Machine (FDGM): A Granular Revolution
Fertilizer disc granulation machines (FDGMs) have emerged as game-changers in the fertilizer industry, revolutionizing the way fertilizers are produced and applied. These machines employ a unique disc-based granulation process to create uniform, high-quality fertilizer granules that enhance crop yield and minimize environmental impact.
Understanding the Disc Granulation Process
The FDGM process consists of several key steps:
-
Mixing: Fertilizer raw materials, including nutrients, binders, and other additives, are thoroughly mixed to create a uniform blend.
-
Granulation: The blended mixture is fed onto a rotating disc, where it is sprayed with a binder solution. The binder helps agglomerate the fine particles into larger granules.
-
Spheronization: As the granules rotate on the disc, they are subjected to centrifugal force, which causes them to take on a spherical shape.
-
Drying: The granules are then dried in a separate chamber to remove excess moisture and ensure they are free-flowing.
-
Cooling: Finally, the dried granules are cooled to room temperature before being packaged and stored.
Advantages of Fertilizer Disc Granulation Machines
FDGMs offer numerous advantages over traditional fertilizer production methods, including:
-
Uniform Granule Size: FDGMs produce consistent, uniform granules that facilitate even distribution and nutrient release, improving crop growth and yield.
-
Enhanced Nutrient Efficiency: Granulated fertilizers have a higher nutrient concentration, resulting in more efficient nutrient uptake by plants.
-
Reduced Dust and Loss: Granulation reduces dust formation and wind loss, minimizing environmental impact and maximizing fertilizer utilization.
-
Improved Storage and Handling: Granulated fertilizers are less prone to moisture absorption and degradation, ensuring longer shelf life and easier handling.
-
Customized Formulations: FDGMs allow for precise control over granule composition, enabling customized fertilizers tailored to specific crop needs.
Applications of Fertilizer Disc Granulation Machines
FDGMs have diverse applications in the fertilizer industry, including:

-
Production of NPK (Nitrogen-Phosphorus-Potassium) Fertilizers: These are the most widely used fertilizers, providing essential nutrients for crop growth.
-
Production of Urea-Based Fertilizers: Urea is a popular nitrogen source, and FDGMs can convert it into granulated forms for enhanced efficiency.
-
Production of Specialty Fertilizers: FDGMs can produce various specialty fertilizers, such as slow-release fertilizers, micronutrient fertilizers, and organic fertilizers.
-
Granulation of Industrial Materials: FDGMs are also used in other industries to granulate materials such as catalysts, detergents, and pharmaceuticals.
Market Trends and Future Prospects
According to a recent study by Grand View Research, the global market for fertilizer disc granulation machines is projected to reach USD 1.5 billion by 2028, growing at a CAGR of 5.4% over the forecast period. This growth is driven by increasing fertilizer consumption, rising demand for high-quality fertilizers, and government initiatives promoting sustainable agriculture practices.
Major market players include:

- Andritz
- ThyssenKrupp
- Buhler
- IFFCO
- Yara International
Customer Perspectives and Questions
- How can FDGMs improve fertilizer efficiency and reduce nutrient loss?
- What are the specific advantages of granulated fertilizers over traditional forms?
- Can FDGMs be used to produce specialized fertilizers for niche crops?
- What are the key factors to consider when selecting an FDGM?
- How can I optimize the operation and maintenance of my FDGM?
Effective Strategies for Fertilizer Disc Granulation Machine Production
-
Implement rigorous quality control measures to ensure consistent granule size and nutrient content.
-
Utilize advanced process control systems to automate and optimize the granulation process.
-
Invest in regular maintenance to minimize downtime and extend the lifespan of the FDGM.
-
Conduct ongoing research and development to explore new applications and improve efficiency.
-
Partner with experienced manufacturers who provide comprehensive technical support and after-sales services.
Tips and Tricks for Fertilizer Disc Granulation Machine Operation
-
Pre-mix the raw materials thoroughly to ensure uniform granule composition.
-
Adjust the binder concentration to achieve the desired granule size and strength.
-
Control the disc speed and rotation time to optimize granule sphericity and drying efficiency.
-
Monitor temperature and humidity levels in the drying chamber to prevent over-drying or under-drying.
-
Use a dedicated cooling system to ensure granules reach room temperature before packaging.
Comparative Tables
Table 1: Comparison of Fertilizer Disc Granulation Machines
Feature |
Machine A |
Machine B |
Machine C |
Disc Diameter |
3 meters |
2.5 meters |
4 meters |
Production Capacity |
10 tons per hour |
8 tons per hour |
12 tons per hour |
Power Consumption |
100 kW |
80 kW |
120 kW |
Price |
USD 1 million |
USD 900,000 |
USD 1.2 million |
Table 2: Advantages and Disadvantages of Fertilizer Disc Granulation Machines
Advantages |
Disadvantages |
Uniform granule size |
High energy consumption |
Enhanced nutrient efficiency |
Bulky equipment |
Reduced dust and loss |
Require skilled operators |
Improved storage and handling |
Can be noisy |
Customized formulations |
Limited granule shape options |
Table 3: Nutrients Applied by Fertilizer Disc Granulation Machines
Nutrient |
Fertilizer Type |
Nitrogen |
Ammonium nitrate, urea |
Phosphorus |
Triple superphosphate, diammonium phosphate |
Potassium |
Potassium chloride, potassium sulfate |
Magnesium |
Magnesium sulfate |
Sulfur |
Ammonium sulfate, elemental sulfur |
Table 4: Applications of Fertilizer Disc Granulation Machines in Various Industries
Industry |
Application |
Fertilizer |
Production of NPK fertilizers, urea-based fertilizers, and specialty fertilizers |
Petrochemical |
Production of catalysts for oil refining |
Pharmaceutical |
Granulation of active pharmaceutical ingredients |
Detergent |
Production of detergent granules |
Conclusion
Fertilizer disc granulation machines are essential tools for the fertilizer industry, transforming the way fertilizers are produced and used. These machines create high-quality, uniform granulated fertilizers that enhance crop yield, reduce environmental impact, and meet the growing demand for sustainable agriculture practices. By understanding the principles, advantages, and applications of FDGMs, fertilizer manufacturers can optimize their production processes and contribute to the global effort towards food security and environmental conservation.
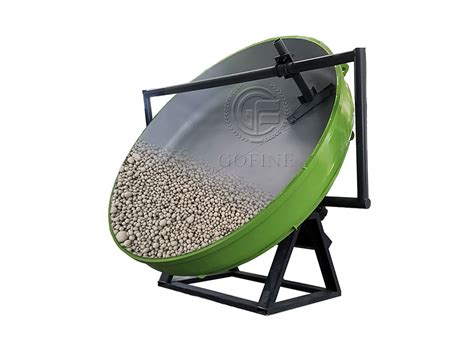:%20A%20Granular%20Revolution)