Magnesium Silicate Double Rolle Granulator Machine: 2023 Ultimate Buyer's Guide
Introduction
Magnesium silicate is a versatile material used in various industries, including pharmaceuticals, food, and construction. Its unique properties, such as its high porosity and absorption capacity, make it suitable for applications such as anticaking agents, excipients, and absorbents. However, producing magnesium silicate granules with consistent size and properties can be challenging. This is where the magnesium silicate double rolle granulator machine comes into play.
What is a Magnesium Silicate Double Rolle Granulator Machine?
A magnesium silicate double rolle granulator machine is a specialized equipment designed to produce granules from magnesium silicate powder. It consists of two counter-rotating rollers with adjustable gap settings. The powder is fed into the nip point of the rollers, where it is compressed and granulated. The resulting granules are then discharged from the machine.
Benefits of Using a Magnesium Silicate Double Rolle Granulator Machine
Using a magnesium silicate double rolle granulator machine offers several benefits:
-
Consistent Granule Size: The machine ensures precise control over the granule size, resulting in uniform and consistent granules.
-
High Production Capacity: Double rolle granulators have high production capacities, making them suitable for large-scale production.
-
Energy Efficiency: These machines are energy-efficient, consuming less power compared to other granulation methods.
-
Compact Design: Double rolle granulators have a compact design, making them easy to install and operate in confined spaces.
-
Low Maintenance: They require minimal maintenance and are easy to clean, reducing downtime and maintenance costs.
Factors to Consider When Choosing a Magnesium Silicate Double Rolle Granulator Machine
When selecting a magnesium silicate double rolle granulator machine, several factors should be considered:
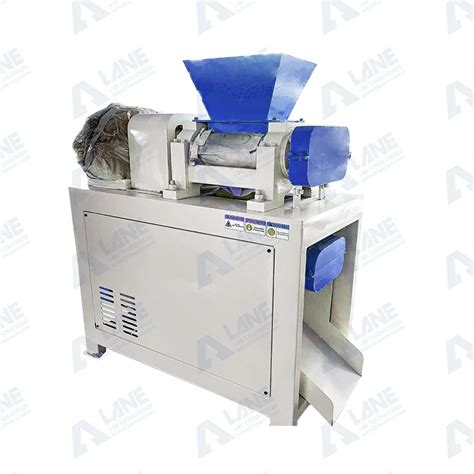
-
Production Capacity: Determine the required production capacity based on your specific application.
-
Granule Size Requirements: Specify the desired granule size range to ensure the machine meets your specifications.
-
Material Compatibility: Ensure that the machine is compatible with magnesium silicate powder and any other materials that may be used in the granulation process.
-
Roller Design: Choose rollers with appropriate surface properties and gap adjustment capabilities to suit your granulation needs.
-
Motor Power: The motor power should be sufficient to handle the required production capacity and material characteristics.
Innovative Applications of Magnesium Silicate
Beyond its traditional uses, magnesium silicate is gaining attention in innovative applications, including:

-
Battery Separator: Magnesium silicate's high porosity and absorption capacity make it a promising material for use as a separator in lithium-ion batteries.
-
Water Filtration: Magnesium silicate can be used as a filter media for removing impurities from water, thanks to its high absorption capacity.
-
Cosmetics: Magnesium silicate is incorporated into cosmetics as an absorbent and mattifying agent, controlling skin shine and improving texture.
Tips and Tricks for Operating a Magnesium Silicate Double Rolle Granulator Machine
-
Proper Feed Control: Ensure a consistent and controlled feed rate of magnesium silicate powder into the machine.
-
Optimal Roller Settings: Adjust the roller gap and pressure settings to achieve the desired granule size and properties.
-
Maintain Cleanliness: Regularly clean the machine and its components to prevent contamination and ensure optimal performance.
-
Regular Inspection: Inspect the machine regularly for wear and tear, and replace worn parts as needed.
-
Training: Train operators on proper operation and maintenance to ensure safe and efficient operation.
Common Mistakes to Avoid
-
Overloading: Avoid overloading the machine to prevent damage and ensure consistent granule quality.
-
Insufficient Drying: Ensure that the granules are sufficiently dried before storage or further processing to prevent moisture absorption and caking.
-
Poor Maintenance: Neglecting regular maintenance can lead to decreased performance, increased downtime, and safety hazards.
-
Incorrect Roller Settings: Improper roller settings can result in non-uniform granule size distribution or poor compaction.
-
Mixing Incompatible Materials: Do not mix incompatible materials with magnesium silicate powder, as this can affect the granulation process and product quality.
Conclusion
The magnesium silicate double rolle granulator machine is an essential equipment for producing consistent and high-quality magnesium silicate granules. By considering the factors discussed in this guide, you can select the right machine for your specific application. With its benefits and innovative applications, this machine is a valuable investment for industries seeking to optimize their granulation processes and explore new possibilities.