Round Disk Granulator: 2023 Comprehensive Guide for Perfect Granulation
Introduction:
In the pharmaceutical and chemical industries, granulation plays a crucial role in transforming powders into granules. Among the various granulation techniques, round disk granulators have emerged as a preferred choice due to their versatility, efficiency, and consistent performance. This comprehensive guide delves into the world of round disk granulators, providing insights into their mechanism, advantages, applications, and key considerations for optimal operation.
Mechanism of Round Disk Granulator:
Round disk granulators utilize a rotating disk and a stationary plow to agglomerate fine particles into granules. The disk rotates at a high speed, creating a centrifugal force that propels the powder particles outward. The stationary plow, positioned close to the disk's edge, scrapes the particles off the disk, causing them to collide and adhere to one another. This process continues until the desired granule size and properties are achieved.
Advantages of Round Disk Granulator:
-
Uniform Granules: Round disk granulators produce granules with a uniform size and shape, ensuring consistent quality and performance in downstream processes.
-
High Efficiency: The high rotational speed of the disk enables efficient granulation, reducing processing time and maximizing production output.
-
Flexible Operation: Round disk granulators can handle a wide range of materials, including powders of varying densities and flowability, making them versatile for different applications.
-
Easy Cleaning and Maintenance: Round disk granulators are designed with ease of cleaning and maintenance in mind, minimizing downtime and ensuring optimal performance.
Applications of Round Disk Granulator:
Round disk granulators find diverse applications in the pharmaceutical, chemical, and food industries. Some of the key applications include:

-
Pharmaceutical Industry: Production of tablets, capsules, and granules for drug delivery.
-
Chemical Industry: Granulation of catalysts, pigments, and other chemical powders for various applications.
-
Food Industry: Granulation of food ingredients, such as flavorings, spices, and additives, to enhance product quality and shelf life.
Key Considerations for Optimal Operation:
To ensure optimal performance of round disk granulators, several key considerations must be addressed:
-
Disk Speed: The rotational speed of the disk significantly influences the granule size and distribution. A higher speed results in smaller granules, while a lower speed produces larger granules.
-
Plow Angle: The angle of the stationary plow relative to the disk affects the granule shape and density. A lower angle creates denser granules, while a higher angle produces less dense granules.
-
Liquid Binder: The type and amount of liquid binder used impact the granule strength and porosity. Proper selection and optimization of the binder are crucial for achieving desired granule properties.
-
Powder Characteristics: The properties of the powder being granulated, such as particle size, density, and flowability, influence the granulation process and final granule characteristics.
Round Disk Granulator Market Overview:
The global round disk granulator market is projected to reach USD 465 million by 2025, growing at a CAGR of 5.4%. This growth is attributed to the rising demand for uniform and high-quality granules in various industries. Factors such as increasing pharmaceutical production, technological advancements, and stringent regulatory requirements drive the market's growth.
Leading Manufacturers of Round Disk Granulator:
- GEA Pharmatech
- Alexanderwerk
- Eirich
- Hosokawa Alpine
- Frewitt
- Sejong Industrial
- Pengfei Mechanical
- Jaygo
- JCT Machinery
- Huanghe Heavy Machinery
Tips and Tricks for Round Disk Granulator Operation:
-
Optimize Disk Speed and Plow Angle: Determine the ideal disk speed and plow angle based on the desired granule size and density. Start with recommended settings and fine-tune the parameters as needed.
-
Control Liquid Binder Addition: Gradually add the liquid binder to the powder while monitoring the granule formation. Avoid excessive binder addition, which can lead to wet granules and poor flowability.
-
Consider Powder Properties: Understand the characteristics of the powder being granulated, such as particle size distribution and flowability. Adjust process parameters accordingly to accommodate different powder properties.
-
Clean and Maintain Regularly: Regular cleaning and maintenance of the round disk granulator ensure optimal performance and prevent contamination. Follow manufacturer's recommendations for cleaning and maintenance schedules.
Case Studies:
-
Pharmaceutical Application: A pharmaceutical company implemented a round disk granulator to produce granules for a new tablet formulation. By optimizing granulation parameters, they achieved consistent granule size and improved tablet performance.
-
Chemical Application: A chemical manufacturer used a round disk granulator to produce catalyst granules for a chemical process. The granulator's high efficiency and ability to handle high volumes enabled them to meet their production targets and maintain product quality.
-
Food Application: A food ingredient manufacturer used a round disk granulator to create uniform granules for flavoring and seasoning blends. The granulation process improved the product's solubility and enhanced its flavor delivery.
Conclusion:
Round disk granulators are versatile and efficient machines that play a crucial role in the production of granules for various industries. By understanding their mechanism, advantages, and key considerations, manufacturers can optimize the granulation process to achieve consistent, high-quality granules. The growing market demand and technological advancements promise continued innovation and improvements in round disk granulator technology, further enhancing its role in the production of diverse granular products.
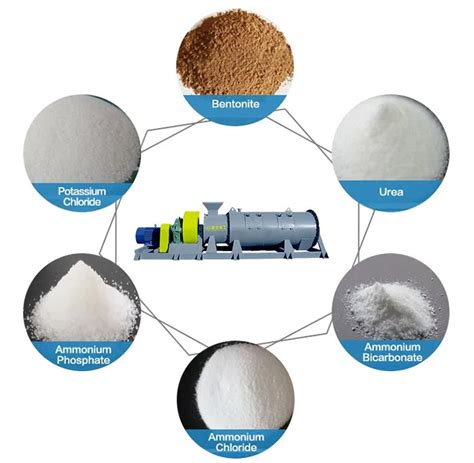
Additional Resources:
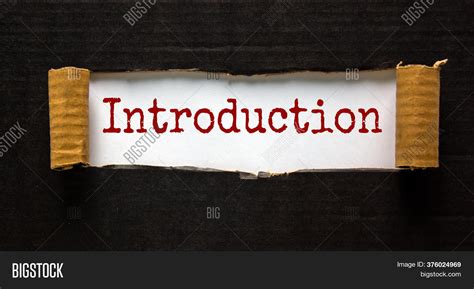