Compound Fertilizer Double Roller Granulator: A Comprehensive Guide to Maximize Productivity
Introduction
Compound fertilizers are widely used in agriculture to enhance crop yields and soil health. Double roller granulators play a vital role in producing these fertilizers by transforming raw materials into uniformly sized granules. This detailed guide delves into the principles of operation, benefits, and optimization strategies for compound fertilizer double roller granulators.
Principle of Operation
Compound fertilizer double roller granulators consist of two rotating rollers with a cylindrical shape. The rollers have a rough surface that creates friction as they rotate. Fertilizer raw materials are fed into the granulator and compressed between the rollers. The resulting material is rolled into granules that are then discharged from the machine.
Types of Compound Fertilizers Produced
Double roller granulators can produce various types of compound fertilizers, including:
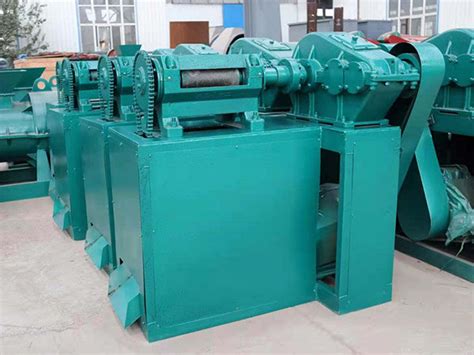
-
NPK fertilizers: These contain nitrogen, phosphorus, and potassium, essential macronutrients for plant growth.
-
Complex fertilizers: These contain a combination of macronutrients and micronutrients, such as sulfur, magnesium, and boron.
-
Controlled-release fertilizers: These release nutrients gradually over an extended period, reducing leaching and environmental impact.
Economic Benefits of Double Roller Granulators
Investing in a compound fertilizer double roller granulator can yield significant economic benefits for producers:

-
Increased yield: Granular fertilizers enhance nutrient uptake, leading to higher crop yields and improved farmer profitability.
-
Reduced labor costs: Double roller granulators automate the granulation process, reducing labor requirements.
-
Improved product quality: Granules produced by rollers have uniform size and shape, ensuring consistent nutrient distribution and enhancing crop performance.
-
Reduced shipping and storage costs: Granular fertilizers are easier to handle, transport, and store, resulting in lower logistical expenses.
Key Factors for Maximizing Productivity
To maximize the productivity and efficiency of compound fertilizer double roller granulators, several key factors must be considered:
Raw Material Properties
-
Particle size: Smaller particle sizes facilitate better granulation.
-
Moisture content: Optimal moisture levels (typically 5-15%) promote granulation and prevent dust formation.
-
Binder selection: Binders, such as lignin sulfonates or polymers, enhance granule cohesion.
Granulator Parameters
-
Roller speed: Adjust the speed to balance granule size and capacity.
-
Roller gap: Setting the correct gap is crucial for controlling granule size and preventing blockage.
-
Roll pressure: Applying appropriate roll pressure ensures proper compression and granulation.
Process Monitoring and Control
-
Moisture monitoring: Use sensors to measure moisture levels and make adjustments as needed.
-
Temperature control: Granulation temperature should be maintained within a specific range to prevent over-drying or under-drying.
-
Product quality analysis: Regularly test granules for size distribution, nutrient content, and physical properties.
Common Mistakes to Avoid
-
Overloading the granulator: This can lead to uneven granulation and reduced product quality.
-
Using binders excessively: Too much binder can hinder granule growth and reduce porosity.
-
Neglecting maintenance: Regular cleaning and lubrication of the granulator ensure optimal performance.
Why Compound Fertilizer Double Roller Granulators Matter
-
Environmental sustainability: Granulation reduces nutrient loss, minimizing environmental impact.
-
Increased fertilizer efficiency: Granules improve nutrient availability to plants, maximizing fertilizer effectiveness.
-
Agricultural productivity: Granular fertilizers support the growth of healthy crops, ensuring food security.
Benefits of Using Compound Fertilizer Double Roller Granulators
-
High-quality granules: Uniform granules with optimal nutrient distribution.
-
Increased crop yields: Enhanced nutrient uptake and plant growth.
-
Reduced environmental impact: Minimized nutrient loss and improved soil health.
-
Increased fertilizer efficiency: Maximized nutrient utilization by plants.
New Applications of Compound Fertilizer Double Roller Granulators
The versatility of compound fertilizer double roller granulators extends beyond traditional fertilizer production. Innovative applications include:
-
Soil conditioners: Granulated organic matter can improve soil structure and water retention.
-
Urban farming: Granulators can produce fertilizers for rooftop gardens and vertical farms.
-
Biochar production: Granulators can transform biochar into pellets for use as a soil amendment.
Tables
Table 1: Raw Material Properties for Optimal Granulation
Material |
Particle Size (μm) |
Moisture Content (%) |
Urea |
<100 |
5-10 |
Monoammonium Phosphate |
<200 |
8-12 |
Muriate of Potash |
<150 |
2-5 |
Table 2: Common Binders Used in Double Roller Granulation
Binder |
Type |
Properties |
Lignin Sulfonates |
Natural |
High cohesiveness, low cost |
Starch |
Biodegradable |
Low cost, environmentally friendly |
Polyvinyl Alcohol |
Synthetic |
High strength, water-soluble |
Table 3: Typical Granulator Parameters for Compound Fertilizers
Parameter |
Range |
Roller Speed (rpm) |
50-120 |
Roller Gap (mm) |
2-5 |
Roll Pressure (MPa) |
0.5-1.5 |
Table 4: Benefits of Using Compound Fertilizer Double Roller Granulators
Benefit |
Description |
High Uniformity |
Granules with consistent size and nutrient content |
Enhanced Nutrient Uptake |
Improved plant growth and crop yields |
Reduced Nutrient Loss |
Minimized environmental impact |
Increased Fertilizer Efficiency |
Maximized nutrient utilization by plants |