Roll Granulator: Your Ultimate Guide to 10x Your Granulation Efficiency
Roll Granulators: Revolutionizing the Pharmaceutical and Food Industries
Roll granulators have emerged as indispensable tools in the pharmaceutical and food industries, transforming the art of granulation. With their ability to produce consistent, uniform granules, these machines pave the way for enhanced product quality, improved flowability, and reduced drying times.
What is Roll Granulation?
Roll granulation is a process that utilizes two rotating rolls to compact and agglomerate powder particles into granules. The rolls generate high shear forces, causing the particles to adhere and form spherical or cylindrical granules.
Benefits of Roll Granulation
Roll granulators offer a myriad of benefits, including:
-
Enhanced Granule Quality: Produces consistent, uniform granules with controlled size distribution and porosity.
-
Improved Flowability: Granules exhibit excellent flowability, minimizing issues during filling and packaging operations.
-
Reduced Drying Times: Granules possess reduced surface area and enhanced porosity, facilitating faster drying.
-
Increased Bulk Density: Granulation increases the bulk density of powders, improving handling and storage efficiency.
How Roll Granulators Work
Roll granulators operate on a simple principle:
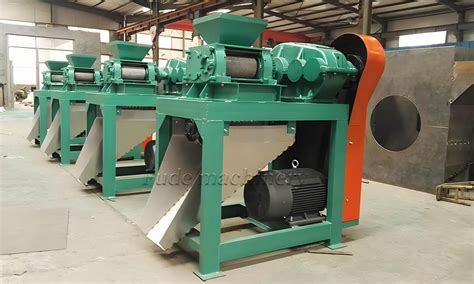
-
Powder Feeding: Powder is fed into the nip point between two rotating rolls.
-
Shear Forces: The rolls rotate in opposite directions, generating high shear forces that cause the particles to deform and adhere.
-
Granule Formation: As the powder undergoes compression, it agglomerates into granules.
-
Granule Discharge: The formed granules are discharged from the granulator.
Roll Granulator Design
Roll granulators consist of various components:
-
Rolls: Made of durable materials like steel or rubber, the rolls rotate to generate shear forces.
-
Roll Gap: The distance between the rolls determines the granule size and porosity.
-
Feeding Mechanism: Ensures a consistent supply of powder to the roll nip point.
-
Granule Collection System: Collects and separates the formed granules from the roll gap.
Roll Granulator Specifications
Roll granulators are characterized by several key specifications:

-
Roll Diameter: Typically ranges from 100 mm to 1500 mm.
-
Roll Width: Dictates the granulator's production capacity.
-
Speed: Controls the shear forces and granule size.
-
Gap Setting: Adjusts the porosity and size of the granules.
Choosing the Right Roll Granulator
Selecting the appropriate roll granulator requires careful consideration of factors such as:

-
Product Characteristics: Consider the powder's properties, granulation requirements, and desired granule attributes.
-
Production Capacity: Determine the required output volume to match your manufacturing needs.
-
Granule Size Distribution: Choose a granulator that can produce granules within the desired size range.
-
Budget: Establish a realistic budget and explore cost-effective granulation solutions.
Roll Granulator Applications
Roll granulators find diverse applications across industries:
-
Pharmaceuticals: Granulation of active pharmaceutical ingredients (APIs) to improve bioavailability, compressibility, and dissolution.
-
Food: Production of powdered food ingredients, such as spices, seasonings, and confectionery fillings, with improved dissolution and texture.
-
Chemicals: Granulation of chemical powders to enhance handling, storage, and reactivity.
Roll Granulator Market Analysis
The global roll granulator market is projected to reach $3.5 billion by 2027, growing at a CAGR of 6.5%. The increasing demand for high-quality granules in pharmaceuticals, food, and other industries drives market growth.
Common Roll Granulation Mistakes to Avoid
- Insufficient powder feeding: Causes inconsistent granule formation and poor granulation efficiency.
- Excessive roll gap: Produces weak granules with poor flowability.
- Too high roll speed: Can lead to particle attrition and granule breakage.
- Ineffective cleaning: Granulator contamination compromises product quality and granulation effectiveness.
Step-by-Step Roll Granulation Process
-
Powder Preparation: Dry and sieve the powder to remove impurities and ensure particle size uniformity.
-
Granulator Setup: Calibrate the roll gap, speed, and feeding rate according to the desired granule specifications.
-
Granulation: Feed the powder into the granulator and monitor the granulation process.
-
Granule Drying: Dry the granules to reduce moisture content and enhance their flowability.
-
Granule Screening: Screen the granules to obtain the desired size range.
Innovations in Roll Granulation
Continuous advancements in roll granulation technology have introduced novel concepts:
-
Twin-Screw Granulation: Combines the advantages of roll granulation with twin-screw extrusion for improved granulation efficiency.
-
Fluidized Bed Roll Granulation: Granulation occurs in a fluidized bed environment, offering enhanced granule sphericity and reduced attrition.
-
Melt Granulation: Utilizes melted binders to create granules with controlled release properties, particularly in pharmaceuticals.
Table 1: Roll Granulator Manufacturers and Models
Manufacturer |
Model |
Roll Diameter (mm) |
Roll Width (mm) |
Speed (rpm) |
Alexanderwerk |
APK |
150-500 |
200-1500 |
5-200 |
GEA |
PharmEx |
100-1500 |
100-1200 |
10-150 |
Hosokawa |
Micro |
100-250 |
100-600 |
10-200 |
NETZSCH |
MicroMax |
150-500 |
200-1200 |
10-150 |
Table 2: Roll Granulator Features and Benefits
Feature |
Benefit |
Variable Speed |
Versatility for granulating different materials |
Adjustable Roll Gap |
Control over granule porosity and size |
Automated Cleaning |
Minimal downtime due to easy cleaning |
PLC Control |
Precise granulation parameter management |
Dust Extraction |
Safe operation and reduced environmental impact |
Table 3: Roll Granulation Applications and Industries
Application |
Industry |
API Granulation |
Pharmaceuticals |
Food Ingredient Granulation |
Food and Beverage |
Chemical Powder Granulation |
Chemicals and Minerals |
Ceramic Powder Granulation |
Ceramics and Glass |
Coal Beneficiation Granulation |
Mining |
Table 4: Roll Granulator Specification Comparison
Parameter |
Roll Granulator A |
Roll Granulator B |
Roll Granulator C |
Roll Diameter |
250 mm |
150 mm |
300 mm |
Roll Width |
600 mm |
400 mm |
800 mm |
Speed |
10-150 rpm |
5-100 rpm |
15-200 rpm |
Production Capacity |
500 kg/hr |
250 kg/hr |
1000 kg/hr |
"Granulation Unraveled: Ask Yourself These Questions for Optimal Results"
- Are my powders dry and free of impurities?
- Have I calibrated the roll gap and speed accurately?
- Is my production capacity aligned with the chosen granulator?
- Can I establish effective cleaning procedures to minimize contamination?
- Have I considered innovative granulation techniques to enhance granule properties?
"Conclusion: Amplify Your Granulation Efficiency"
Roll granulators have revolutionized granulation processes, elevating product quality, flowability, and efficiency. By embracing the latest advancements and adhering to best practices, you can unlock the full potential of roll granulation and drive significant improvements in your manufacturing operations.
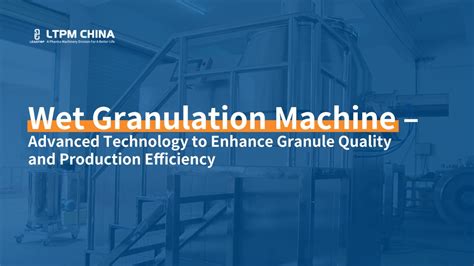