Ammonium Sulphate Granulator Machine: The Ultimate Guide to Increase Efficiency and Productivity
Introduction:
In the agricultural industry, maximizing crop yields and soil fertility are primary concerns. Nitrogenous fertilizers, such as ammonium sulfate, play a crucial role in fulfilling these objectives. However, conventional production methods of ammonium sulfate result in fine particles that pose challenges in handling, storage, and application. To overcome these challenges, ammonium sulfate granulator machines have emerged as innovative solutions, transforming the industry with their ability to produce high-quality, granulated fertilizer.
Pain Points:
- Dust generation and handling difficulties associated with fine ammonium sulfate particles
- Inconsistent granule size and shape, affecting fertilizer application efficiency
- Caking and agglomeration during storage, leading to reduced usability
- Suboptimal fertilizer distribution due to uneven particle size
Motivations:
- Enhance fertilizer handling and reduce environmental impact
- Improve fertilizer application precision and maximize nutrient uptake
- Minimize storage issues and preserve fertilizer quality
- Increase crop yields and optimize soil health
Benefits of Ammonium Sulphate Granulator Machine:
- Produces uniform, spherical granules with controlled size and shape
- Eliminates dust generation, ensuring a cleaner and healthier work environment
- Reduces caking and agglomeration, improving storage stability
- Facilitates precise fertilizer application, reducing waste and increasing efficiency
- Enhances nutrient uptake by plants, maximizing crop yields
Key Features and Specifications:
-
Capacity: Ranges from 1 ton per hour (TPH) to over 100 TPH, catering to diverse production requirements
-
Pan Diameter: Typically between 1 meter and 6 meters, influencing granulation capacity and efficiency
-
Power Requirement: Varies depending on capacity, ranging from 15 kW to over 100 kW
-
Material: Constructed from durable materials such as stainless steel or carbon steel to withstand corrosive environments
-
Granule Size: Adjustable within a specific range, typically between 1 mm and 4 mm, to meet application needs
Working Principle:
Ammonium sulfate granulator machines employ a rotating pan or drum to agglomerate fine ammonium sulfate particles into granules. The pan is inclined at an angle and rotates continuously, creating a centrifugal force that causes the particles to collide and adhere to each other. Water or a binder solution is sprayed onto the particles during the process, promoting bonding and granulation. The granules are then dried and cooled before being discharged from the machine.
Types of Ammonium Sulphate Granulator Machines:
-
Horizontal Pan Granulator: A widely used type, featuring a horizontal pan that rotates on a fixed axis.
-
Inclined Pan Granulator: Similar to the horizontal pan granulator but with an inclined pan that enhances material flow.
-
Vertical Drum Granulator: Employs a vertical drum that rotates on a central axis, suitable for large-scale production.
Common Applications:
- Production of granulated ammonium sulfate fertilizer for agricultural purposes
- Manufacture of industrial chemicals such as ammonium sulfate-based detergents
- Pharmaceutical formulations that utilize ammonium sulfate
Table 1: Comparison of Ammonium Sulfate Granulator Machine Types
Type |
Advantages |
Disadvantages |
Horizontal Pan Granulator |
Simple design, low maintenance |
Lower production capacity |
Inclined Pan Granulator |
Moderate production capacity, improved material flow |
Requires more space |
Vertical Drum Granulator |
Large production capacity, high efficiency |
Complex design, higher maintenance |
Factors Influencing Granulation:
-
Particle Size: Smaller particles facilitate stronger bonding and smoother granules.
-
Moisture Content: Optimal moisture level promotes particle adhesion without excessive caking.
-
Binder Type: Binders enhance bonding and prevent granule disintegration.
-
Rotation Speed: Higher rotation speeds increase centrifugal force, leading to faster granulation.
-
Pan Angle: The angle of the pan influences material flow and granulation efficiency.
Common Mistakes to Avoid:
-
Overloading the Machine: Exceeding the recommended capacity can compromise granulation quality.
-
Incorrect Moisture Content: Too much or too little moisture can lead to poor granule formation or excessive dust generation.
-
Insufficient Binder: Inadequate binder usage can result in weak granules prone to breakage.
-
Improper Maintenance: Neglecting regular maintenance can affect machine performance and reduce granulator lifespan.
-
Inadequate Drying: Insufficient drying can lead to granule moisture problems during storage.
FAQs:
-
What is the typical lifespan of an ammonium sulfate granulator machine?
With proper maintenance, an ammonium sulfate granulator machine can have a lifespan of over 10 years.
-
What are the energy consumption requirements of a granulator machine?
Energy consumption varies depending on capacity, but typically ranges between 15 kW to 100 kW.

-
How does the size of the granulator machine impact production capacity?
Larger granulator machines with wider pans have higher production capacities.
-
What is the ideal moisture content for ammonium sulfate granulation?
Optimal moisture content typically ranges from 5% to 10%, depending on the particle size and binder used.

-
Is it possible to customize the granulator machine to specific requirements?
Yes, many manufacturers offer customization options to meet specific production needs, such as capacity, granule size, and materials of construction.
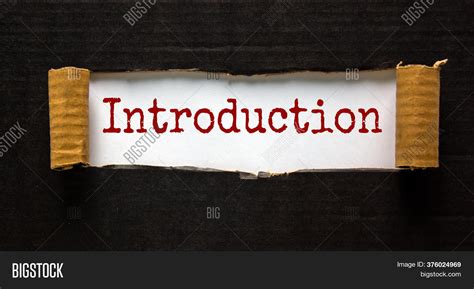
-
What are the safety precautions to observe when operating a granulator machine?
Follow manufacturer instructions, wear appropriate safety gear, and ensure proper ventilation to avoid dust inhalation and other hazards.
Creative New Word:
Granuvate: A novel term coined to describe the innovative process of transforming fine particles into high-quality granules using advanced granulator machines.
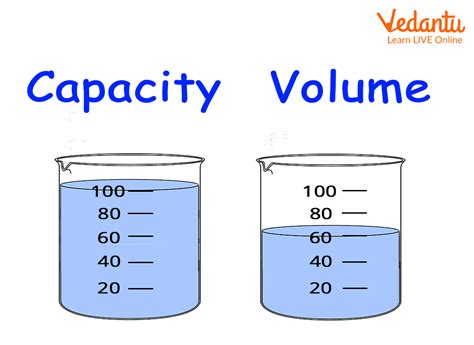
Tables:
Table 2: Key Specifications of Ammonium Sulfate Granulator Machines
| **Specification** | **Range** |
|---|---|
| Capacity | 1 TPH to 100+ TPH |
| Pan Diameter | 1 meter to 6 meters |
| Power Requirement | 15 kW to 100+ kW |
| Granule Size | 1 mm to 4 mm |
Table 3: Benefits of Granulated Ammonium Sulfate Fertilizer
| **Benefit** | **Description** |
|---|---|
| Reduced Dust Generation | Minimizes environmental impact and improves handling safety |
| Uniform Granule Size | Enhances fertilizer application precision and distribution |
| Reduced Caking | Improves storage stability and prevents agglomeration |
| Improved Nutrient Uptake | Promotes efficient uptake of nutrients by plants |
Table 4: Factors Influencing Granulation Efficiency
| **Factor** | **Impact** |
|---|---|
| Particle Size | Smaller particles enhance bonding and granulation |
| Moisture Content | Optimal moisture promotes adhesion without excessive caking |
| Binder Type | Binders strengthen granules and prevent disintegration |
| Rotation Speed | Higher speeds increase centrifugal force and accelerate granulation |
| Pan Angle | Influences material flow and granulation efficiency |