Horizontal Mixers for Every Need: A Comprehensive Guide
Introduction
Horizontal mixers, also known as horizontal ribbon blenders, are versatile and indispensable equipment in various industries, including pharmaceuticals, food processing, chemicals, plastics, and more. Their unique design enables efficient mixing of dry and semi-dry materials, making them a crucial tool for manufacturers seeking optimal product quality.
Types of Horizontal Mixers
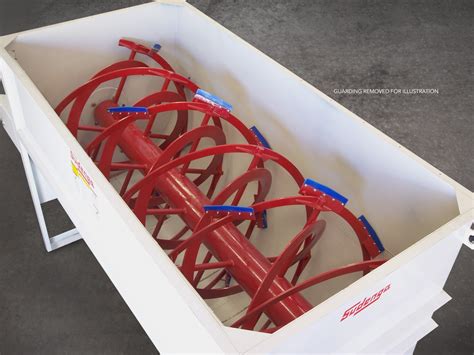
Horizontal mixers come in various types, each suited to specific mixing requirements.
-
Ribbon Blenders: Feature a helical ribbon agitator that moves material in a spiral motion, ensuring thorough mixing.
-
Paddle Mixers: Use paddle-shaped agitators to achieve a gentler mixing action, suitable for delicate materials.
-
Tumble Blenders: Rotate materials in a drum-like container, providing low-shear mixing and high homogeneity.
-
Cone Blenders: Have a cone-shaped vessel with a central agitator, ideal for mixing small batches of powder or granules.
Benefits of Horizontal Mixers

-
Uniform Mixing: Horizontal mixers provide highly uniform mixing, ensuring consistent product quality batch after batch.
-
Versatile Applications: Their ability to mix a wide range of materials makes horizontal mixers suitable for various industries.
-
Large Capacity: Horizontal mixers can handle large volumes of materials, meeting the demands of high-volume production.
-
Gentle Mixing Action: Some types of horizontal mixers, such as paddle mixers, offer a gentle mixing action that preserves material integrity.
Pain Points and Motivations
-
Inconsistent Mixing: Poor mixing can lead to inferior product quality, customer complaints, and lost revenue.
-
Low Efficiency: Inefficient mixing processes can slow down production and increase operating costs.
-
Material Degradation: Aggressive mixing actions can damage delicate materials, compromising product quality.
-
Motivations: Companies seek horizontal mixers to improve mixing quality, increase efficiency, and protect sensitive materials.
Potential Applications
Horizontal mixers have a wide range of potential applications, including:
- Pharmaceutical: Mixing active ingredients, excipients, and filler materials.
- Food Processing: Blending dry ingredients for food products, including spices, flour, and sugar.
- Chemicals: Mixing raw materials for chemical synthesis, fertilizers, and industrial powders.
- Plastics: Combining polymers, colorants, and additives for plastic manufacturing.
- Agriculture: Blending animal feed, fertilizers, and seed treatments.
- Ceramics: Mixing raw materials for ceramic production, including clay, feldspar, and silica.
Technical Specifications
-
Capacity: Ranges from laboratory-scale (a few liters) to industrial-scale (over 100 cubic meters).
-
Materials of Construction: Typically made of stainless steel, carbon steel, or other materials to withstand specific chemical and temperature requirements.
-
Mixing Speed: Determined by material properties and desired mixing time.
-
Agitator Design: Varies depending on mixer type and specific mixing requirements.
-
Discharge Options: Include manual, pneumatic, or automated discharge mechanisms.
Industry Statistics

- The global horizontal mixer market is projected to reach US$ 568.3 million by 2023, with an annual growth rate of 4.6%.
- The food processing industry accounts for the largest share of horizontal mixer sales, followed by the chemical industry.
- Pharmaceutical and other specialty applications are driving the demand for high-performance horizontal mixers.
Comparison of Horizontal Mixers
Feature |
Ribbon Blender |
Paddle Mixer |
Tumble Blender |
Cone Blender |
Mixing Action |
Helical ribbon |
Paddle-shaped |
Drum-like |
Central agitator |
Material Integrity |
Moderate |
High |
Moderate |
Moderate |
Mixing Uniformity |
High |
Medium |
Medium |
Medium |
Suitable Materials |
Dry, semi-dry |
Delicate materials |
Free-flowing |
Powders, granules |
Capacity |
High |
Medium |
Medium |
Small |
Pros and Cons of Horizontal Mixers
Pros:
- Uniform mixing
- Versatile applications
- Large capacity options
- Gentle mixing action available
Cons:
- Can be expensive to purchase and maintain
- May not be suitable for highly viscous materials
- Some models require manual discharge
Recommendations
- Determine the specific mixing requirements for the intended application.
- Consider material properties, mixing volume, and desired mixing uniformity.
- Choose a horizontal mixer with the appropriate agitator design, capacity, and materials of construction.
Conclusion
Horizontal mixers play a crucial role in various industries, enabling efficient and thorough mixing of dry and semi-dry materials. Understanding the different types, benefits, and applications of horizontal mixers can help manufacturers make informed decisions and optimize their production processes. By carefully selecting the right horizontal mixer, companies can enhance product quality, increase efficiency, and meet evolving customer demands.