21 Roll Granulators: An In-Depth Guide for Pharmaceutical and Nutraceutical Applications
Roll Granulation: A Versatile Process for Enhanced Material Properties
Roll granulation is a widely employed technique in the pharmaceutical and nutraceutical industries, offering numerous advantages for the production of high-quality granules. This process involves compressing a powder bed between two counter-rotating rolls, resulting in the formation of granules with enhanced flowability, compressibility, and dissolution properties.
Advantages of Roll Granulation
-
Improved Flowability: Roll granulation significantly enhances the flowability of powders, facilitating efficient handling, filling, and tableting operations.
-
Enhanced Compressibility: The pressure applied during roll granulation increases the density and compressibility of granules, leading to improved tablet strength and reduced friability.
-
Controlled Dissolution: Roll granulation allows for precise control over granule size and density, enabling tailored dissolution profiles for optimal drug release characteristics.
-
Increased Granule Strength: The frictional forces exerted during roll granulation strengthen the inter-particle bonds within granules, resulting in improved mechanical stability and reduced attrition.
-
Reduced Dust Generation: By agglomerating fine powders, roll granulation minimizes dust generation during handling and processing, ensuring a cleaner and safer working environment.
Key Parameters in Roll Granulation
-
Roll Speed: The rotational speed of the rolls influences the granule size and density. Higher roll speeds generally produce smaller granules.
-
Roll Pressure: The pressure applied by the rolls determines the degree of densification and consolidation within the granules.
-
Feed Rate: The rate at which powder is fed into the granulator affects the granule size distribution and moisture content.
-
Granulating Liquid: The choice and amount of granulating liquid (e.g., water, ethanol) play a crucial role in the granulation process, influencing granule properties such as cohesiveness and porosity.
Types of Roll Granulators
There are two main types of roll granulators:
-
Dry Granulators: These machines operate without the addition of a granulating liquid, relying on the pressure applied to consolidate powder particles.
-
Wet Granulators: In wet granulation, a granulating liquid is added to the powder prior to compression, promoting the formation of stronger granule bonds.
Applications of Roll Granulators in Pharmaceuticals and Nutraceuticals
Roll granulation finds widespread application in the production of:
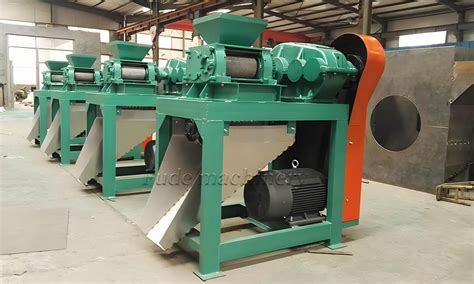
-
Pharmaceutical Tablets: Roll granulation is a critical process in tablet manufacturing, enhancing the compressibility and dissolution properties of active pharmaceutical ingredients (APIs).
-
Nutraceutical Powders: Roll granulation is used to improve the flowability and stability of nutraceutical powders, ensuring consistent dosage and bioavailability.
-
Food Powders: Roll granulation is employed to enhance the solubility and granulation of food powders, including coffee, tea, and cocoa.
Recent Advancements in Roll Granulator Technology
Recent advancements in roll granulator technology have focused on:

-
Innovative Roll Designs: Advanced roll designs, such as grooved or textured rolls, enable more efficient granulation, improving granule properties and reducing energy consumption.
-
Advanced Control Systems: Sophisticated control systems allow for precise monitoring and adjustment of roll speed, pressure, and feed rate, ensuring consistent and reproducible granulation results.
-
Scalability and Automation: Larger-scale roll granulators and automated systems facilitate increased production capacities, reducing labor costs and improving process efficiency.
Case Studies
- According to a study published in the Journal of Pharmaceutical Sciences, roll granulation significantly improved the compressibility and dissolution rate of an API, leading to improved tablet performance.
- A study in the journal Powder Technology demonstrated that roll granulation reduced the dust generation of a nutraceutical powder by over 90%, enhancing product safety and handling efficiency.
- A case study in the International Journal of Food Science and Technology showed that roll granulation enhanced the solubility and granulation of cocoa powder, resulting in improved chocolate beverage quality.
Conclusion
Roll granulation is a versatile and efficient process that offers numerous advantages for the production of high-quality granules in the pharmaceutical and nutraceutical industries. By understanding the key parameters, choosing the appropriate type of granulator, and incorporating recent advancements, manufacturers can optimize their roll granulation processes to achieve desired material properties and meet specific product requirements.
Glossary
-
Granulation: The process of agglomerating fine powders into larger granules.
-
Roll Granulator: A machine that compresses a powder bed between two counter-rotating rolls to form granules.
-
Granule Size: The diameter of individual granules.
-
Granule Density: The mass per unit volume of granules.
-
Friability: The tendency of granules to break down under mechanical stress.
Further Reading