Material Management Air Force: 2023 Guide
Material Management Air Force: A Comprehensive Overview
The Material Management Air Force (MMAF) is a specialized branch of the United States Air Force responsible for managing the acquisition, storage, and distribution of materiel to support Air Force operations worldwide. With a budget of over $12 billion and a workforce of over 100,000 personnel, the MMAF plays a crucial role in ensuring the readiness and sustainability of the Air Force.
Mission and Responsibilities
The primary mission of the MMAF is to provide seamless and efficient materiel management services to enable the Air Force to execute its missions effectively. Key responsibilities include:
-
Acquisition: Planning, procuring, and contracting for materiel to meet the requirements of the Air Force.
-
Storage: Maintaining and managing warehouses and storage facilities to store materiel securely and efficiently.
-
Distribution: Transporting materiel from storage facilities to operational units worldwide, ensuring timely delivery.
-
Inventory Management: Tracking and managing materiel inventory levels to optimize availability and prevent shortages.
-
Maintenance and Repair: Performing preventive and corrective maintenance on equipment and materiel to extend their lifespan and ensure operational readiness.
Challenges and Opportunities
The MMAF operates in a challenging and rapidly evolving environment, facing numerous challenges:
-
Global Supply Chain Disruptions: Disruptions in the global supply chain can impact the availability and cost of materiel, posing significant challenges to the MMAF.
-
Aging Infrastructure: Many of the Air Force's storage and distribution facilities are aging and in need of modernization to meet current and future requirements.
-
Increased Operational Tempo: The Air Force's increased operational tempo in recent years has heightened the demand for materiel and put a strain on the MMAF's resources.
Despite these challenges, the MMAF also recognizes opportunities for improvement:


-
Leveraging Technology: Implementing advanced technologies, such as artificial intelligence and predictive analytics, can streamline operations, improve inventory management, and enhance decision-making.
-
Collaboration and Partnerships: Strengthening partnerships with industry and other government agencies can provide access to new technologies, expertise, and resources.
-
Innovation and Agility: Embracing a culture of innovation and agility will enable the MMAF to adapt quickly to changing operational requirements and technological advancements.
Key Performance Indicators (KPIs) and Metrics
The MMAF utilizes various KPIs and metrics to measure its performance and identify areas for improvement:
-
Materiel Readiness: Percentage of mission-critical materiel available to meet operational requirements.
-
Fill Rate: Percentage of orders filled within a specified timeframe.
-
Inventory Turnover Ratio: Ratio of inventory value to sales or usage, indicating inventory efficiency.
-
Maintenance Downtime: Percentage of time that equipment is unavailable due to maintenance or repairs.
-
Customer Satisfaction: Surveys and feedback from operational units to assess the quality and timeliness of materiel support.
Technologies and Innovations
The MMAF is actively investing in new technologies and innovations to enhance its capabilities and improve operational efficiency:

-
Artificial Intelligence (AI): AI-powered systems are being developed to analyze data, predict future demands, and optimize inventory management.
-
Blockchain: Blockchain technology is being explored to create secure and transparent supply chains, improve traceability, and prevent fraud.
-
3D Printing: 3D printing technology has the potential to reduce lead times and increase the availability of spare parts.
-
Autonomous Vehicles: Autonomous vehicles are being tested to automate material handling and transportation tasks.
-
Virtual Reality (VR): VR is being used for training, simulation, and remote maintenance of equipment.
Future Outlook and Recommendations
The future of material management in the Air Force is expected to be shaped by several key trends:
-
Increased Reliance on Technology: Advanced technologies will continue to play a larger role in automating processes, enhancing decision-making, and improving inventory visibility.
-
Global Supply Chain Evolution: The MMAF must adapt to evolving global supply chains, including the rise of additive manufacturing and the need for resilient networks.
-
Sustainability and Environmental Awareness: The Air Force is committed to reducing its environmental footprint, and the MMAF is exploring sustainable material management practices.
To prepare for the future, the MMAF should consider the following recommendations:
-
Invest in Cybersecurity: Enhance cybersecurity measures to protect sensitive data and critical systems from cyber threats.
-
Foster Collaboration and Partnerships: Strengthen partnerships with industry, academia, and other government agencies to leverage expertise and resources.
-
Develop Agile and Adaptive Supply Chains: Embolden the development of agile and adaptive supply chains that can respond to disruptions and evolving requirements.
-
Continuously Innovate: Create a culture of innovation and experimentation to foster the development of new technologies and streamline operations.
-
Engage with Customers: Regularly seek feedback from operational units to understand their needs and improve material management services.
Materiel Management Air Force: Enhancing Operational Readiness
Improving Inventory Management
Effective inventory management is essential for ensuring that the Air Force has the materiel it needs when and where it is required. The MMAF is implementing various strategies to enhance inventory management:
-
Centralized Inventory Management: Implementing centralized inventory systems to provide real-time visibility into stock levels across the Air Force.
-
Predictive Analytics: Utilizing predictive analytics to forecast demand, optimize inventory levels, and prevent shortages.
-
Just-in-Time (JIT) Inventory: Adopting JIT inventory practices to reduce inventory carrying costs and improve availability.
-
Vendor-Managed Inventory (VMI): Partnering with vendors to manage inventory levels and ensure timely resupply.
Optimizing Supply Chain Management
A seamless and efficient supply chain is crucial for delivering materiel to operational units on time. The MMAF is exploring various initiatives to optimize supply chain management:
-
Supplier Performance Management: Developing supplier performance management programs to evaluate vendor capabilities and ensure reliability.
-
Risk Mitigation: Identifying and mitigating supply chain risks, such as geopolitical instability and natural disasters.
-
Dual Sourcing: Diversifying suppliers for critical items to reduce dependency on single sources.
-
Transportation Optimization: Implementing transportation optimization algorithms to reduce shipping costs and improve delivery times.
Enhancing Maintenance and Repair Services
The MMAF is responsible for maintaining and repairing equipment and materiel to ensure operational readiness. The following initiatives are being pursued to enhance maintenance and repair services:
-
Predictive Maintenance: Utilizing sensors and data analytics to predict equipment failures and schedule maintenance proactively.
-
Centralized Repair Facilities: Establishing centralized repair facilities to improve efficiency and reduce repair times.
-
Remote Maintenance Support: Providing remote maintenance support to operational units to minimize downtime and increase equipment availability.
-
Virtual Reality (VR) for Maintenance: Using VR technology to provide immersive training and enable remote maintenance assistance.
Advancing Technology and Innovation
The MMAF is actively investing in new technologies and innovations to transform material management and improve operational efficiency:
-
Blockchain for Supply Chain Management: Exploring the use of blockchain technology to enhance supply chain transparency, traceability, and security.
-
Artificial Intelligence (AI) for Inventory Optimization: Utilizing AI-powered algorithms to optimize inventory levels, predict demand, and automate replenishment.
-
3D Printing for Spare Parts: Implementing 3D printing to produce spare parts on-demand, reducing lead times and improving availability.
-
Augmented Reality (AR) for Maintenance: Using AR technology to provide step-by-step guidance during maintenance procedures and facilitate remote assistance.
Material Management Air Force: Engaging with Customers
Understanding Customer Needs and Requirements
The MMAF is committed to meeting the needs of its customers, which include operational Air Force units. To ensure customer satisfaction, the following strategies are being implemented:
-
Customer Relationship Management (CRM): Establishing a comprehensive CRM system to track customer interactions, preferences, and feedback.
-
Regular Customer Feedback Collection: Conducting surveys and soliciting feedback from operational units to assess satisfaction levels and identify areas for improvement.
-
Customer Advisory Boards: Forming customer advisory boards to provide input on material management policies and initiatives.
-
Dedicated Customer Support Teams: Providing dedicated customer support teams to assist operational units with materiel-related inquiries and issues.
Enhancing Communication and Transparency
Effective communication and transparency are essential for building strong relationships with customers. The MMAF is committed to:
-
Centralized Information Hub: Establishing a centralized information hub to provide operational units with access to real-time data on materiel availability, delivery schedules, and maintenance status.
-
Regular Communication Updates: Sending out regular communication updates to keep customers informed of material management initiatives, policies, and performance metrics.
-
Open and Honest Dialogue: Fostering an open and honest dialogue with customers to address concerns, resolve issues, and improve services.
-
Social Media Engagement: Utilizing social media channels to connect with customers and share relevant information.
Measuring and Improving Customer Satisfaction
The MMAF recognizes the importance of measuring and improving customer satisfaction:
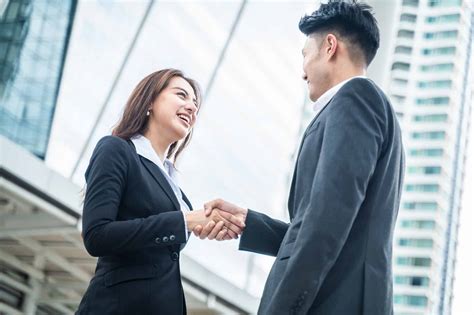
-
Customer Satisfaction Surveys: Regularly conducting customer satisfaction surveys to gauge satisfaction levels and identify areas for improvement.
-
Customer Focus Groups: Holding customer focus groups to gather in-depth feedback and understand evolving needs.
-
Net Promoter Score (NPS): Utilizing the Net Promoter Score (NPS) metric to measure customer loyalty and identify opportunities for improvement.
-
Continuous Improvement: Continuously reviewing customer feedback and implementing improvements to enhance customer satisfaction over time.
Tables
Table 1: Key Performance Indicators (KPIs) for Material Management Air Force
KPI |
Description |
Materiel Readiness |
Percentage of mission-critical materiel available to meet operational requirements |
Fill Rate |
Percentage of orders filled within a specified timeframe |
Inventory Turnover Ratio |
Ratio of inventory value to sales or usage, indicating inventory efficiency |