4500 KGPH Granulation Machines: Revolutionizing Pharmaceutical Manufacturing
Granulation Machine: The Heart of Pharmaceutical Manufacturing
In the pharmaceutical industry, granulation machines play a pivotal role in the production of tablets and capsules. Granulation is the process of agglomerating fine powders into larger, more stable granules, enhancing their flowability, compressibility, and dissolution rate. Granulation machines, ranging from 4500 KGPH to smaller capacities, are essential equipment for achieving consistent and high-quality drug products.
Benefits of 4500 KGPH Granulation Machines
-
High Production Capacity: 4500 KGPH granulation machines boast an impressive production capacity, allowing for efficient and large-scale manufacturing of pharmaceutical products.
-
Improved Granule Quality: These machines precisely control the granulation process, ensuring uniform granule size, porosity, and density, which directly impact drug delivery performance.
-
Cost Reduction: High production capacity and efficient operation reduce production costs and improve overall profitability.
-
GMP Compliance: 4500 KGPH granulation machines adhere to current Good Manufacturing Practices (GMP), guaranteeing product safety and quality.
Applications of Granulation Machines
Granulation machines find applications in various pharmaceutical manufacturing processes, including:
-
Tablets: Granules formed by granulation machines are directly compressed into tablets.
-
Capsules: Granules can be encapsulated into capsules for oral administration.
-
Controlled-Release Formulations: Granules can be engineered to release drugs over time through sustained or targeted delivery systems.
-
Topical Formulations: Granules can be incorporated into creams, ointments, and gels for topical drug delivery.
Key Features of 4500 KGPH Granulation Machines
-
Large Mixing Chamber: The spacious mixing chamber ensures thorough and uniform mixing of powders and liquids.
-
Advanced Granulation Technology: Utilize various granulation methods, such as high-shear wet granulation, fluidized-bed granulation, or extrusion-spheronization.
-
Automated Controls: PLC-based control systems allow precise monitoring and adjustment of granulation parameters, such as speed, temperature, and moisture content.
-
CIP/SIP Capability: Cleaning-in-place (CIP) and sterilization-in-place (SIP) capabilities ensure product integrity and equipment cleanliness.
Market Size and Industry Trends
The global granulation machine market is projected to reach $1.5 billion by 2027, driven by rising demand for pharmaceuticals worldwide. The increasing prevalence of chronic diseases and the growing popularity of personalized medicine contribute to this growth.
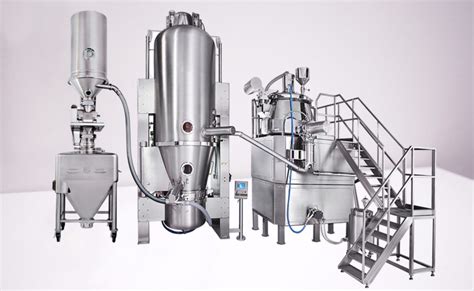
Innovative Applications for Granulation Machines
Beyond traditional pharmaceutical applications, granulation machines are finding new uses in other industries:
-
Food and Beverage: Granulation technology enhances food textures and flavors, improves solubility, and reduces waste.
-
Cosmetics: Granules can be used as exfoliating agents, absorbents, or carriers for active ingredients in skin and hair care products.
-
Agriculture: Granulation techniques improve fertilizer efficiency, soil structure, and seed germination.
Tips and Tricks for Effective Granulation
-
Optimize Powder Characteristics: Control particle size distribution, moisture content, and surface properties of powders to ensure successful granulation.
-
Select the Right Binder: Choose the appropriate binder based on the desired granule properties, drug solubility, and release profile.
-
Control Process Parameters: Precisely monitor and adjust temperature, mixing speed, and liquid addition rate to achieve consistent granule quality.
-
Evaluate Granule Properties: Conduct thorough testing to assess granule size, porosity, flowability, and disintegration time to ensure optimal performance.
Common Mistakes to Avoid in Granulation
-
Overgranulation: Excessive granulation can lead to hard, dense granules with poor flowability and dissolution properties.
-
Undergranulation: Insufficient granulation results in friability, poor compression, and disintegration problems.
-
Insufficient Binder Concentration: Inadequate binder levels compromise granule stability and may result in granule breakage.
-
Improper Drying: Incomplete or uneven drying can lead to moisture-sensitive granules prone to degradation or microbiological growth.
Conclusion
4500 KGPH granulation machines are indispensable equipment in the pharmaceutical industry, enabling efficient and high-quality production of tablets, capsules, and other dosage forms. By embracing advanced technologies, innovative applications, and best practices, manufacturers can harness the full potential of granulation machines to deliver safe and effective drug products.
Frequently Asked Questions
-
How do granulation machines affect drug bioavailability? Granulation improves granule porosity and surface area, enhancing drug dissolution and absorption.
-
What are the different types of granulation machines available? High-shear granulators, fluidized-bed granulators, and twin-screw extruders are commonly used granulation machines.
-
How can granulation machines be integrated into continuous manufacturing processes? Modern granulation machines can be seamlessly integrated into continuous manufacturing lines for increased efficiency and reduced production time.
Tables for Quick Reference
Granulation Method |
Advantages |
Disadvantages |
High-Shear Wet Granulation |
High speed and efficiency |
Can generate heat and shear stress |
Fluidized-Bed Granulation |
Gentle on particles |
May require longer processing times |
Extrusion-Spheronization |
Produces spherical granules |
Requires specialized equipment |
Granule Properties |
Significance |
Measurement Methods |
Granule Size |
Affects flowability, compressibility, and dissolution rate |
Sieving, laser diffraction |
Porosity |
Influences granule density and dissolution |
Mercury intrusion porosimetry, gas pycnometry |
Flowability |
Determines ease of handling and tablet filling |
Angle of repose, Carr's index |
Pharmaceutical Applications |
Granulation Type |
Key Benefits |
Tablets |
High-Shear Wet Granulation |
High compressibility, uniform drug distribution |
Capsules |
Fluidized-Bed Granulation |
Controlled particle size, reduced dust formation |
Controlled-Release Formulations |
Extrusion-Spheronization |
Targeted drug delivery, improved patient compliance |
Granulation Industries Beyond Pharmaceuticals |
Applications |
Benefits |
Food and Beverage |
Texture enhancement, flavor improvement |
Increased consumer appeal, reduced waste |
Cosmetics |
Exfoliation, absorption, active ingredient delivery |
Improved skin and hair health, enhanced product appeal |
Agriculture |
Fertilizer efficiency, soil structure improvement |
Enhanced crop yields, environmental sustainability |