7 Essential Granulation Machine Features for Maximizing Your Pharmaceutical Production
What is a Granulation Machine?
A granulation machine is an essential piece of equipment in the pharmaceutical industry. It is used to create granules, which are small, spherical particles that are used in the production of tablets, capsules, and other dosage forms. Granules are typically made from a dry powder, which is mixed with a binder and then passed through the granulation machine. The machine granulates the powder by applying pressure to it, causing it to form into small, spherical particles.
Why is Granulation Important?
Granulation is an important process in the pharmaceutical industry because it has several benefits, including:
-
Improved flowability: Granules are more free-flowing than powders, which makes them easier to handle and process. This can lead to increased efficiency and productivity in the manufacturing process.
-
Increased uniformity: Granules are more uniform in size and shape than powders, which can help to ensure that the final dosage form is of consistent quality.
-
Improved stability: Granules are less likely to degrade than powders, which can help to extend the shelf life of the final dosage form.
How Does a Granulation Machine Work?
A granulation machine works by applying pressure to a dry powder, causing it to form into small, spherical particles. The machine typically consists of a rotating drum or bowl that is filled with the powder. The drum or bowl is then rotated, causing the powder to be compacted and granulated.
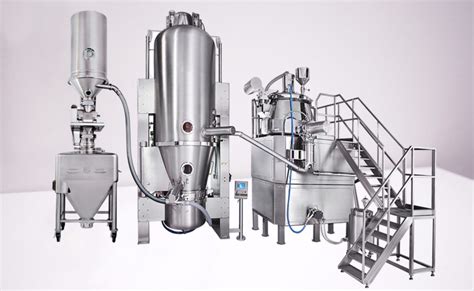
The granulation machine can be equipped with a variety of different tools and attachments, which can be used to control the size, shape, and density of the granules. The machine can also be equipped with a heating or cooling system, which can be used to control the temperature of the granules.

7 Essential Granulation Machine Features
When choosing a granulation machine, it is important to consider several key features. These features include:
-
Capacity: The capacity of the granulation machine refers to the amount of powder that it can process at one time. The capacity of the machine will depend on the size of the drum or bowl, as well as the speed of rotation.
-
Granulation rate: The granulation rate refers to the speed at which the machine can produce granules. The granulation rate will depend on the speed of rotation of the drum or bowl, as well as the size of the granules.
-
Granule size: The granule size refers to the size of the granules that are produced by the machine. The granule size will depend on the size of the holes in the screen that is used to granulate the powder.
-
Granule shape: The granule shape refers to the shape of the granules that are produced by the machine. The granule shape will depend on the shape of the tools that are used to granulate the powder.
-
Density: The density of the granules refers to the weight of the granules per unit volume. The density of the granules will depend on the type of powder that is used, as well as the amount of pressure that is applied to the powder.
-
Moisture content: The moisture content of the granules refers to the amount of water that is contained in the granules. The moisture content of the granules will depend on the type of powder that is used, as well as the temperature at which the granules are dried.
-
Uniformity: The uniformity of the granules refers to the consistency of the granules in terms of size, shape, and density. The uniformity of the granules will depend on the type of powder that is used, as well as the settings of the granulation machine.
Common Mistakes to Avoid When Using a Granulation Machine
There are several common mistakes that can be made when using a granulation machine. These mistakes can lead to problems with the quality of the granules, as well as the efficiency of the manufacturing process. Some of the most common mistakes include:

-
Using the wrong type of powder: The type of powder that is used will have a significant impact on the quality of the granules. It is important to use a powder that is of a consistent quality and that is free of impurities.
-
Overfilling the granulation machine: Overfilling the granulation machine can lead to problems with the flow of the powder and the formation of granules. It is important to fill the machine to the correct level, as specified by the manufacturer.
-
Using the wrong speed: The speed of rotation of the drum or bowl will have a significant impact on the size and shape of the granules. It is important to use the correct speed, as specified by the manufacturer.
-
Not using the correct tools: The tools that are used to granulate the powder will have a significant impact on the size and shape of the granules. It is important to use the correct tools, as specified by the manufacturer.
-
Not drying the granules properly: The granules must be dried properly before they can be used in the manufacturing process. If the granules are not dried properly, they can be unstable and can cause problems with the quality of the final dosage form.
4 Useful Tables for Granulation Machine Users
The following tables provide some useful information for granulation machine users.
| Table 1: Granulation Machine Capacity |
|---|---|
| Machine Type | Capacity (kg/h) |
|---|---|
| Small | 10-50 |
| Medium | 50-100 |
| Large | 100-500 |
| Table 2: Granulation Rate |
|---|---|
| Machine Type | Granulation Rate (kg/min) |
|---|---|
| Small | 1-5 |
| Medium | 5-10 |
| Large | 10-20 |
| Table 3: Granule Size |
|---|---|
| Screen Size (μm) | Granule Size (μm) |
|---|---|
| 500 | 500-1000 |
| 250 | 250-500 |
| 125 | 125-250 |
| Table 4: Granule Density |
|---|---|
| Material | Density (g/cm3) |
|---|---|
| Sugar | 1.5 |
| Starch | 1.4 |
| Cellulose | 1.3 |